Viscose fiber:
It is a semi-synthetic fiber which was earlier known as viscose rayon. Viscose Rayon made from natural sources of regenerated cellulose; such as wood, bamboo and related agricultural products. It has the same molecular orientation like cellulose. Rayon fabrics used widely and in huge demand showing to its special characteristics, like high strength with soft and comfortability.
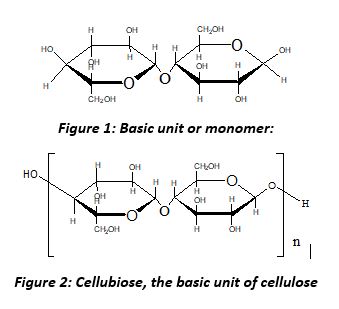
n = 175, cellubiose unit for Viscose
n = 250, cellubiose unit for Cuprammonuim
n = 300, cellubiose unit for Polynosic
History behind rayon production:
Famous British chemist Charles Frederick Cross and his collaborators Edward John Bevan and Clayton Beadle patented their artificial silk in the year of 1894. They named it as “viscose”, because its production is associated with an intermediate state of a highly viscous solution. The Viscose rayon was first commercially produced by the U.K. Company Courtaulds Fibers in 1905. In 1910, American Viscose, a division of Courtaulds fibers was formed to produce their formulation in the United States. The name “rayon” was accepted in 1924, from this time viscose being used for the viscous organic liquid used to make rayon.
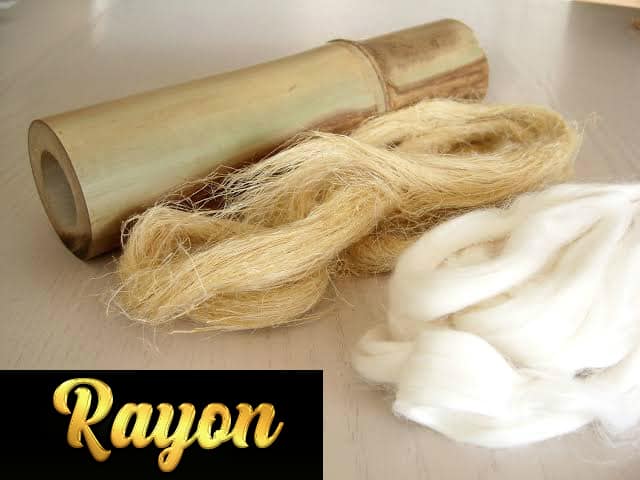
What is Regenerated fiber?
The fiber which we obtained by conversion of natural fiber through chemical processes is termed as regenerated fiber. The regenerated fibers are classified into the following four groups —
I) Cellulosic fibers – Viscose Rayon.
II) Cellulosic esters – Acetate, triacetate.
III) Protein fibers – Casein.
IV) Miscellaneous – Alginate, Rubber.
Chemical reaction involves in viscose rayon production: Regeneration sequence:
Step-1: At first wood are chopped into small pieces and processed into cellulose pulp. Then the cellulose pulp is treated with a 17.5% solution of NaOH which converts it into soda-cellulose.
Cell – OH + NaOH Cell – ONa + H2O
(Cellulose) (Soda cellulose)
Step-2: The soda cellulose reacts with carbon disulphide (CS2) to form sodium cellulose xanthate [C6H7O2(OH)2OCS2Na]
Cell – ONa + CS2 Cell – O – CS2Na
(Soda cellulose) (Sodium cellulose xanthate)
Step-3: Sodium cellulose xanthate as dissolved in a dilute solution of caustic soda and its form orange honey like liquid.
Step-4: This liquid extruded into sulphuric acid (H2SO4) which regenerates the cellulose now in the form of long filaments called viscose rayon.
Cell – O – CS – SNa + H2SO4 Cell – OH + Na2SO4
(Sodium cellulose xanthate) (Regenerated cellulose)
This point key modification such as changing the shape and size of the cross section well co-operative attitude can be made.
Viscose fiber manufacturing process:
1. Wood pulp preparation:
At first the bark of the wood is removed and chipped into small pieces about inches. Then the chips are treated with Calcium bi sulphite [Ca(HSO)2] and the treated chips then processed with steam under pressure for about 14 hours. These treatments do not highly affect the cellulose but it decomposes and solubilizes the smearing substances. After that purification of the cellulose. Finally bleached with hypochlorite and converted into boards or sheets of paper.
2. Steeping & Pressing:
The boards or sheets of paper contain about 90 to 94% of pure cellulose. Primarily conditioning in a room at a definite humidity and temp. This conditioning is compulsory. Vertically stacking and pressing, the boards or sheets are soaked in a 17.5% solution of caustic soda for approximately 1-4 hrs. This process is known as Steeping. Then a hydraulic ram in the press for the excess alkali processing.

3. Shredding:
The shredding m/c comprises a drum inside which whirl a pair of blades with serrated edges. The shredders are cooled with water and will take 200 lbs of pressed soda cellulose at a time. In approximately two or three hours they break it up into very fine “Crumbs” (break into very small parts).
4. Ageing:
With the completion of shredding, the crumbs are aged. They are preserved in a galvanized vessel with a cap and through oxidation with atmospheric oxygen, degradative changes took place. Some depolymerization occurs and the degree of polymerization falls from about 780 to 360 in this process. With the increase in the temperature, the aging goes rapidly – that’s the process of de-polymerization.
5. Churning:
After completion of ageing, the soda cellulose (Cell – ONa) crumbs are initiated into rotating air-tight hexagonal churns. Approximately 10% of their own (crumbs) weight of carbon disulphide (CS2) is introduced and the crumbs and disulphide are churned up together into a deep orange, gelatinous mass of [C6H7O2(OH)2OCS2Na] sodium cellulose Xanthate is formed. Churning is continued for approximately 3 hrs, the churns revolving at about 2 rpm.
6. Mixing (Solution):
Through the mixing of sodium cellulose xanthate [C6H7O2(OH)2OCS2Na] with dilute caustic soda for approximately 4 to 5 hrs by stirring, the vessel being cooled. The xanthate dissolves to a clear-brown, viscous liquid, like honey. This liquid is known as “Viscose” but is still too impure, and too young to spin.
7. Ripening:
Storing of the viscose solution for 4 to 5 days at 10o-18oC and during this time it ripens. Meanwhile the viscosity at first falls, but afterward rises, so that by the time the solution is ready to spin. The viscose ripening test for spun ability is given below –
Acetic acid test: The viscose solution will dissolve in 40% acetic acid solution before it ripens, but when it is ripe the viscose will precipitate in this solution.
8. Spinning:
Basically Two types of spinning process. They are:
1) Discontinuous: (a) Pot/cake spinning
(b) Bobbin spinning
2) Continuous: (a) Nelson spinning
(b) American process of industrial rayon corporation.
Solution preparation: Solution for spinning comprises with the following substances-
· Water(H2O)-69%
· Zinc sulphate(ZnSO4)-1%
· Sodium sulphate(Na2SO4)-18%
· Glucose (C₆H₁₂O₆) -2%
· Sulphuric acid (H2SO4)-10%
Sodium sulphate (Na2SO4) precipitates the cellulose xanthate [C6H7O2(OH)2OCS2Na]. The sulphuric acid (H2SO4) transforms xanthate into cellulose, carbon disulphide (CS2) and sodium sulphate (Na2SO4). Glucose (C₆H₁₂O₆) provides softness and pliability and zinc sulphate (ZnSO4) contributes in strength addition.
Filtration: Filtration for the removal of undissolved materials that might cause disruption in smooth spinning process.
Wet spinning: At first, the ripened viscose solution passes through a centrifugal pump. After some processing the solution is forced through a spinneret mostly made of platinum alloys and having many fine holes with diameters ranging from 0.05-0.1 mm. The jet of viscose enters a coagulating bath containing the composition of mixture. The operation in coagulating bath follows two routes to convert regenerated cellulose-
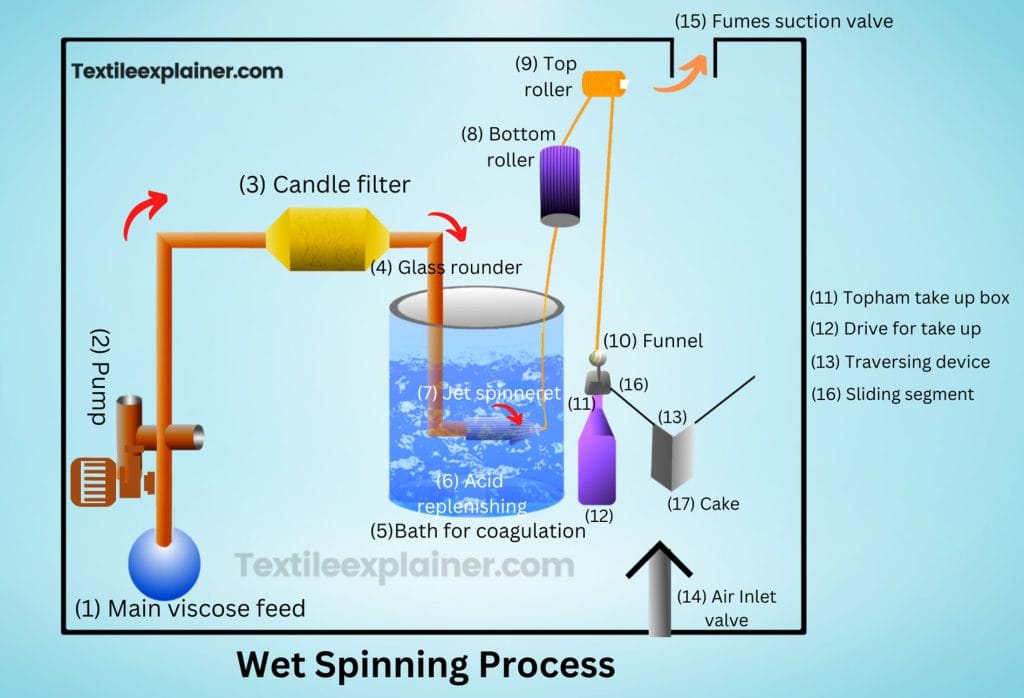
(1) Main viscose feed (2) Pump (3) Candle filter (4) Glass rounder end (5)Bath for coagulation
(6) Acid replenishing pipe selection (7) Jet spinneret (8) Bottom godet roller (9) Top godet roller
(10) Funnel for smooth processing (11) Topham take up box (12) Drive for take up
(13) Traversing device (14) Air Inlet valve (15) Fumes suction valve (16) Sliding segment
(17) Cake
After the spinning bath operation, it passed through two rollers to the topham box. Topham box is the take up device for cake spun viscose rayon.
9. Purification:
The collected yarn in the Topham Box is not pure and relatively weak. So it has to be purified. Purification process basically comprises of 5 operations-
I) Washing
II) Desulfurizing
III) Bleaching
IV) Conditioning
V) Drying
The first wash is with water, the second is with Sodium sulphide (Na2S) solution to remove Sulphur and possible compounds of Sulphur residual from the Xanthate. For complete whitening, so it is treated with a slightly alkaline solution of a sodium hypochlorite to bleach it. This is followed by a wash with dilute hydrochloric acid for conditioning and a final wash with water. After that, the cakes are dried. Finally coning of viscose rayon done and go through the process of shipping.
Quality of viscose rayon depends on the following factors:
1.Spinning bath temperature.
2. Spinning bath composition.
3.Coagulation speed of the filaments.
4. Immersion speed of the filaments in the spinning bath.
5. Spinning speed.
6. Imparted stretch to the filaments.
Physical properties of viscose rayon:
1. Moisture absorption:
Viscose rayon absorbs moisture more than cotton; the moisture content of viscose rayon is about 13% at 65% R.H. and 70oF Temp.
2. Tensile strength:
The fiber in dry condition has more strength than the wet condition. The tensile strength of viscose rayon is 1.5 to 2.4 GPD (gram per denier) in the dry state and 0.7-1.2 GPD in the wet state. For high tenacity viscose rayon, the corresponding values are 3-4.6 GPD and 1.9-3.0 GPD respectively.
3. Elasticity:
Elasticity of viscose rayon is less than 2-3% after which creep develops and permanent elongation sets in until the yarn breaks.
4. Elongation at break:
Ordinary viscose rayon has 15-30% elongation at break while high tenacity rayon has only 9-17% elongation at break when the yarn is wet; it is easy to stretch and has higher elongation – 20-35% for ordinary and 14-20% for high tenacity viscose.
5. Density: 1.5 gm/cc.
6. Specific gravity: 1.5.
7. Melting temp: Do not decompose approximately at (176o-204o) C.
8. Resiliency: Low.
9. Dimensional stability: High for HWM.
10. Flammability: Flammable and burning is like cotton.
Chemical properties of viscose fiber:
1. Effect of acid: Acids like Sulphuric acid, Hydrochloric acid etc. reacts with the viscose rayon and produce hydrocellulose. Cold acid solutions for short time do not attack viscose rayon. If the temp is not high, acids like euphoric, hydrochloric and nitric acid can also be used in strong concentrations. It is attacked by hot dilute or cold concentrated mineral acids which diminishes and deteriorate the fiber.
2. Effect of alkali: Weak alkali does not disrupt viscose, whereas concentrated alkali will cause swelling and reducing the strength.
3. Effect of solvent: Resistance to organic solvents.
4. Effect of bleaching: Though viscose rayon can withstand both oxidizing and reducing bleaches, it can be attacked by strong oxidizing bleaches.
5. Biological agents: (Action of microorganism) Microorganisms like molds, mildew, bacteria etc. impact on the color, strength, dyeing property and luster of rayon. Clean and dry viscose rayon is rarely attacked by mold and mildew.
6. Action of light: Prolonged exposure to sunlight weakens viscose rayon. This weakening is due to moisture and Ultra Violet light of the sunlight and % loss of strength or exposure to Ultra Violet light.
7. Action of heat: Viscose rayon becomes yellowish color at long exposure to high temperature. Approximately at 3000F (1500C) or more, viscose rayon loses its strength and begins to crumble at 3500 -4000F.
8. Dye ability: Better affinity for dyes than cotton. Applied dyes – Vat, Direct, and Sulphur.
9. Conductivity: Good conductor of heat.
10. Flammability: Burns rapidly.
Commercial Name of Viscose:
· Zantral
· Avril
· Fibro HSO
· Grasim
High Tenacity viscose rayon: Research of the spinning of rayon has been intensive and unceasing. Every aspect of viscose production and spinning has been studied and increased understanding of the factors involved has made possible the production of rayons with characteristics that are suited to particular application. The most important of these are the high tenacity rayon.
High tenacity viscose rayons are –
I) Tenasco
II) Cordura
III) Durafil
IV) Forfisan
Process of high tenacity viscose rayon:
1) Maintaining a higher than usual degree of polymerization in the cellulose.
2) Frequent change of filter cloth for better filtration.
3) Stretching the fiber before it is set, usually as much as 150% as maximum stretch.
4) The coagulating bath containing more zinc than usual. The presence of high concentration of zinc ions imparts coagulation of the xanthate on the skin and this hamper regeneration of the cellulose. Thus giving time for the stretching to be carried out.
5) Because color and dye ability are unimportant in type yarn, removal of sulphur from the yarn is unnecessary in fact, it the sulphur is left in it may help the bonding of fibre to rubber.
6) Use modifiers in spun bath.
7) Two spinning bath twice.
Special viscose:
Evlan: A viscose rayon staple fiber used for carpet trade. The cross-section is smoother than standard viscose. Rayon has a higher crimp usual. It has a higher strength than usual and this gives durability. It has been widely used since 1962. Evlan is used for Carpets.
Topel: A cross-section cellulosic fiber. It swells very little, as it has much less affinity for water. Good resistance to caustic alkali. Useful in package dyeing. Blending with cotton gives better appearance, handle and drape.
End Uses of Viscose rayon:
The softness, drape and the luster in the fiber make it a preferred choice for ladies garments and menswear. The most common uses of viscose are in apparel like-
· Dresses
· Suits
· Sari
· Lingerie
· Children cloths
· Umbrella cloths
· Protective cloths
· Sewing embroidery threads
· Curtains
· Cushions
· Beach wear
· Sports wear
· Nonwoven fabrics of baby wipes, wet wipes and napkins etc.
Differences between Polyester and Viscose:
While many consider the viscose and polyester to be similar, there are a lot of differences between the two materials.
1. Both polyester and rayon are made from long fibers but polyester is a synthetic fiber whereas viscose is semi-synthetic that is using natural fibers but chemicals in the process.
2. Polyesters are more moisture wicking while viscose is more absorbent.
3. Polyester dries faster and does not wrinkle as easily as viscose.
4. Polyester is stronger and does not shrink.
5. Viscose is more likely to pill, where polyester resists abrasion.
6. Polyester is made from petroleum oil; while viscose is made from plants.
7. Viscose fiber is biodegradable while most of the polyester fibers are not biodegradable.
8. Polyester production and use contribute to pollution around the world.
MUSFIQUR RAHMAN
86 thoughts on “viscose fiber manufacturing process”
Nice work keep it up!
Thanks a lot.
to much helpful
Hope you like it Mahmud.
The way you explain a complex topic in an easy-to-understand way is really impressive. Specially the part” Viscose Fiber Manufacturing Process” is well explained .
Thanks my dear student.Hope you have gained some knowledge on Viscose.
introduction of viscose fiber is very easy to understand.very helpful.
Thanks Sagor.
To Much Helpful Topic
Sir ❤️
Thanks Shihab.
Nice explanation
appreciate your concern.
We have learned details about viscose from history to usage. One of the best aspects of this article is that one can easily get a very clear idea about viscose
Thanks Naim
Honestly, the writing is great. I didn’t have any idea about viscose. I learned a lot after reading it, although after a while I don’t remember it anymore, but I enjoyed reading it. Especially when I read the Wood pulp preparation part, I thought it was easy to make.
Thanks Rashed.
Love everything you write. After reading the article my confusion differences between Polyester and Viscose is now cleared.
This article gives us a clear concept about viscose fiber. Especially its manufacturing process and chemistry.
Thanks Ismam for your valuable comment.
Thank you so much for sharing such an informative article!
Specially, the High Tenacity Viscose Rayon and Special Rayon part took my interest.
Thanks Ibrahim
Honestly, the writing is great. I Don’t have any idea about viscose fiber.I learned a lot after reading it.Especially when i read the wood pulp preparation part,i Through it was easy to make.
Hope you have enjoyed the article.
From this content/ video easily understand the viscose manufacturing process. And i gathered knowledge about viscose & polyester.Now we can easily identify the differences between viscose and polyester. In a fabric more viscose will make it more comfortable as viscose being a regenerated cellulose has properties like cellulosic, more polyester will make it better crease resistant and durable but not comfortable as it is a 100% manmade fiber.
Thanks for your valuable comment Zhumu.
From this content/ video easily understand the viscose manufacturing process. And i gathered knowledge about viscose & polyester.Now we can easily identify the differences between viscose and polyester. In a fabric more viscose will make it more comfortable as viscose being a regenerated cellulose has properties like cellulosic, more polyester will make it better crease resistant and durable but not comfortable as it is a 100% manmade fiber.
Thanks for your valuable comment Zhumu.
Special viscose (Evlan & Topel)
This topic is my favourite.
I am not clear about charning
A rotating air-tight hexagonal churns where sodium cellulose xanthate formed.
Thanks for shearing this.very imformative.
Thanks dear.
Fabrics of viscose fibers are easily dyed and have excellent hygienic properties (hygroscopicity), which is especially important in goods made for popular use. The accessibility of raw materials and the low cost of the chemical reagents, as well as the satisfactory textile properties and broad possibilities for modification, ensure that viscose fibers are economical to produce and widely used.
Wow you are in the right track.
Very informative article.
Thanks a lot Soumen.
Keep up good work . it’s really good textile explainer
Appreciate your concern.
Excellent sir
Thanks my student.
Though this topic is so much hard to understand but now it’s like so much easy to understand now because of your valuable easy explained.
Thanks a lot.
Thanks my dear student Alhaj.
Excellent article sir. You cleared my all of confusion
Thanks Rafiq.
excellent article sir.Best of luck sir.
Best article on polyester fiber ever!
Thanks my dear student Abed.
I learned a lot from this article.
Appreciate your concern.
Excellent articles sir.Which I was able to understand very easily.
Thanks my student Siam
Fantastic article.
Hope you like it.
fantastic article.
Thanks Hafsa.
the topic is very important
Appreciate your valuable comment.
This topic or content is very useful for us to understand about viscose fiber manufacturing easily..
It helps us in future to job sector..
Thank you sir…
welcome my dear student.
A weak student can get easily understand about viscose fiber manufacturing to read your topic or see video about it..
Carry on sir…
Best whishes for you…
Thanks.
Thanks dear.
Very helpfull article, thank you so much sir.
welcome my dear.
Welcome my dear student.
We have learned details about viscose from history to usage. One of the best aspects of this article is that one can easily get a very clear idea about viscose.
Thanks Sultan.
Appreciate your comment.
It’s an educative lesson for all.
Thanks a lot
It was very informative specially “Differences Between Polyester And Viscose” this part was very helpful for me to understand the dissimilarity between poly and viscose
Thanks a lot Moshfikur.
It was very informative specially “Differences Between Polyester And Viscose” this part was very helpful for me to understand the dissimilarity between poly and viscose . I have learned a lot by reading this article
Thanks Rafi.
Thank you sir for this enlightening article about viscose.
Sir, I have a question. Viscose rayon and Silk Viscose. Are they same?
Thanks a lot dear student.Viscose rayon and silk completely two different things.one is regeneration and the other is natural.
Thank you sir for this information.
It,s really important parts for textile parts.This topics increased our textile knowledge.
Tnx sadiq sir..
Very helpfull article, thank you so much sir.
Very helpfull article, thank you so much sir.❤️❤️
Very helpfull article, thank you sir.❤️❤️
this is a nice post
Very helpful article
Excellent article sir💯
Thanks Durjoy.
Nice work Sir keep it up!
Thanks for the compliment.